Ceramic coatings: the two techniques
Depending on your requirements, there are two types of ceramic coating we can offer: thermal spraying and thermochemical coating.
These techniques apply a coating to a surface to optimise existing properties or to add new ones. They can also protect the part from phenomena such as wear, corrosion, erosion, etc.
Ceramic coating produced by thermal spraying
Using this technique, although the particles are sprayed at high speed, the substrate is not deformed and its structure is unchanged.
The coating may consist of oxides, metals, carbides and/or any other type of composite.
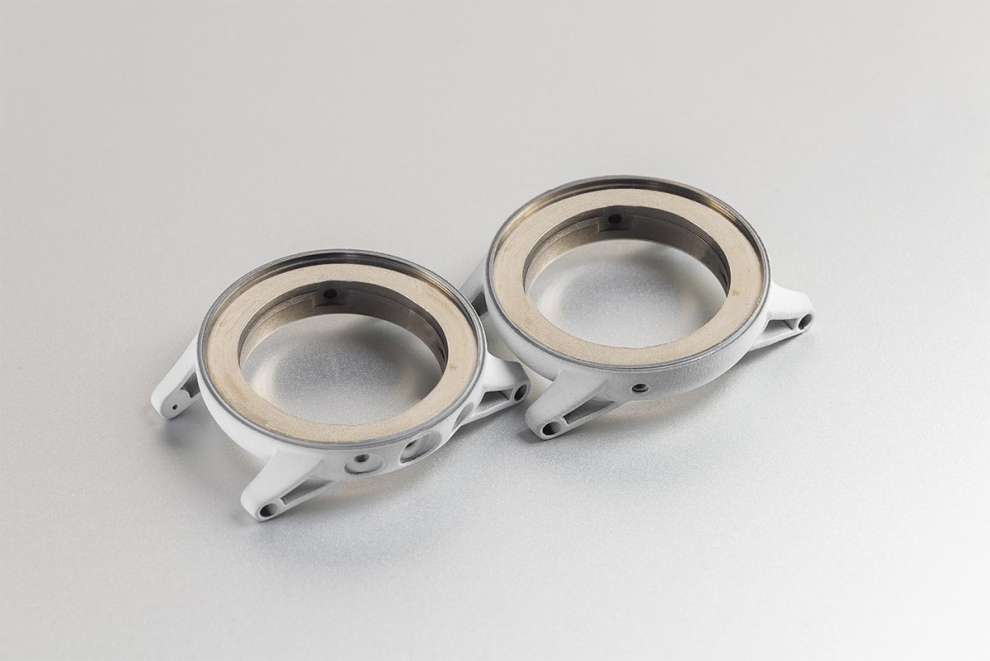
Metal watch case body coated with white ceramic by thermal spraying.
The spraying process creates surface roughness, the degree of which depends on the porosity of the ceramic.
Thermochemical ceramic coating
Unlike a coating produced by spraying, this process does not generate any surface porosity and the coating is harder than that produced by thermal spraying.
This technique is very commonly applied to parts exposed to extremely corrosive environments, which need to be very well sealed and possibly very hard.
It also offers the benefit of being suitable for coating inside diameters (bored holes).
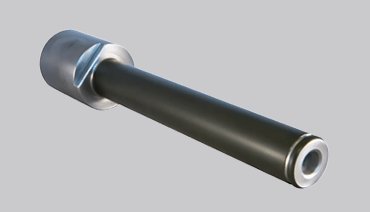
A metal cylinder coated with a ceramic applied by a thermochemical process, with no surface porosity.
Some features of these two coating processes:
Thermal spraying | Thermochemical | |
Thickness | 150 to 400 µm | 50 to 100 µm |
Surface porosity | 2 to 4 % | 0 |
Density of the ceramic | 96 to 98 % | 100 % |
Hardness | Up to 1,300 HV | Greater than 1800 HV |
Finishing operations may be performed on ceramic-coated parts (grinding or machining) which do not impair the functional capabilities of the coating.
Our expertise
Do you have a particular project in mind?
Is there a question you would like to ask?We look forwarding to hearing from you and working with you!
Contact us!